
The source factory
Makes you stand out!
"Where your concepts are elegantly brought to life through masterful craftsmanship and innovation."
Detailed Description of the OEM/ODM Process at YiYi Sexy Lingerie Factory in Foshan
-
As a brand company, you and our team will jointly conduct market research to understand the target market's needs, trends, competition, and customer preferences. This step helps both parties determine the product's style, design, and functional requirements.
-
You provide product design sketches or concepts, and YiYi Factory's design team will turn these ideas into detailed design plans, including fabric selection, color combinations, style details, and production techniques. You can also choose from our existing designs, as our design team creates 2-3 new designs daily. We also provide technical support during this phase to ensure the designs are feasible for production.
-
we create samples. Typically, several rounds of revisions and feedback are required until you're fully satisfied. During this phase, we review the samples to ensure the following: proper fit, design elements and appearance, functionality of the production techniques, and whether they are suitable for manufacturing.
-
YiYi Factory procures materials according to the approved samples and material specifications. We ensure that all materials meet quality and environmental standards and that we have sufficient stock to fulfill production needs.
-
YiYi Factory moves into mass production. The key to this phase is ensuring that every step of the production process meets the brand's quality standards and delivery timelines. We arrange a detailed production plan for you, coordinating production lines, staff, and equipment resources.
More Details …
-
Throughout the production process, we implement several quality control checkpoints, including material inspection, semi-finished product inspection, and final product inspection. We also welcome you to send representatives for sample inspections to ensure that each batch meets your quality standards.
-
After production, our factory will handle packaging according to your specified requirements. This step may include custom brand labels, hang tags, and special packaging needs.
-
YiYi Factory will arrange the transportation and delivery of products according to your needs. The logistics process may involve various transportation methods (such as air or sea freight) and customs clearance at the destination.
-
After delivery, the factory maintains communication with you to monitor the product’s market performance and customer feedback. Based on this feedback, we may need to make product improvements or adjustments to better meet the end customer’s needs and increase customer satisfaction.
-
Many sexy lingerie brands, after extensive research, choose to collaborate with a strong manufacturer like YiYi Factory. After the initial cooperation, brands appreciate YiYi's competitive pricing and reliable delivery capabilities. This mutual trust leads to a long-term partnership, resulting in more stable product quality, guaranteed delivery times, and a competitive edge in the market for both parties.
Customized Lingerie, Easy!
Welcome to Yiyi , You turn complexity into simplicity in just 3 steps!
1、Tell Us What You Need
Tell us as specific as possible of your needs, provide the drawing, reference picture and share your idea.
2、Get Solution & Quote
We will work on the best solution according to your requirements, the specific quote will be provided within 24 hours.
3、Approve for Mass Production
We will start mass production after getting your approval and deposit, and we will handle the shipment.
— Yiyi factory
YiYi OEM Process
Minimum Order Quantity
Lower minimum order quantities, offer greater production flexibility.
It’s not easy for customers to find a sexy lingerie manufacturer that offers ultra-low minimum order quantities, but at Yiyi Factory, you can place an order with just 300 pieces of a single color and style.
Many customers report difficulty in finding stable, high-quality suppliers for small-batch orders, due to the 20+ intricate processes involved in lingerie production, which makes manufacturing and quality control quite complex.
Since 2014, we have overcome various challenges to provide tailored OEM and ODM solutions for e-commerce platforms and international brand companies, offering samples within 3-7 days.
Whether you prioritize cost-effectiveness or top-tier quality, we can quickly deliver high-quality products at any scale, with customized production to meet your specific needs.
Additionally, our collection of 2,800 classic designs supports custom color and size variations. In some cases, ample stock allows us to ship on the same day your order is placed.
Yiyi Factory’s Efficient
Quality Management
Process:
1. Design and Development Quality Control:
Design Review: Collaboratively review design drawings, samples, and specifications to ensure feasibility and alignment with customer needs.
Sample Creation & Testing: Develop and test samples for comfort, washability, and colorfastness to meet final product standards.
2. Material Procurement Quality Control:
Supplier Evaluation: Carefully select and evaluate fabric and accessory suppliers to ensure quality and environmental standards.
Material Inspection: Inspect incoming materials for color, elasticity, texture, and OEKO-TEX certification compliance.
3. Production Quality Control:
Pre-production Preparation: Clarify production processes and ensure workers understand quality standards.
In-process Monitoring: Continuously inspect each production stage and adjust if needed.
Equipment Maintenance: Regularly maintain and calibrate machinery to prevent deviations.
4. Final Inspection & Packaging Quality Control:
Final Product Inspection: Check finished products for appearance, craftsmanship, functionality, and size accuracy.
Packaging Inspection: Ensure flawless products are packaged correctly, with durable, waterproof materials for safe transit.
5. After-sales Quality Control:
Customer Feedback: Invite factory inspections and track customer feedback for quick resolution of quality issues.
Continuous Improvement: Use after-sales data to improve production management and quality standards.
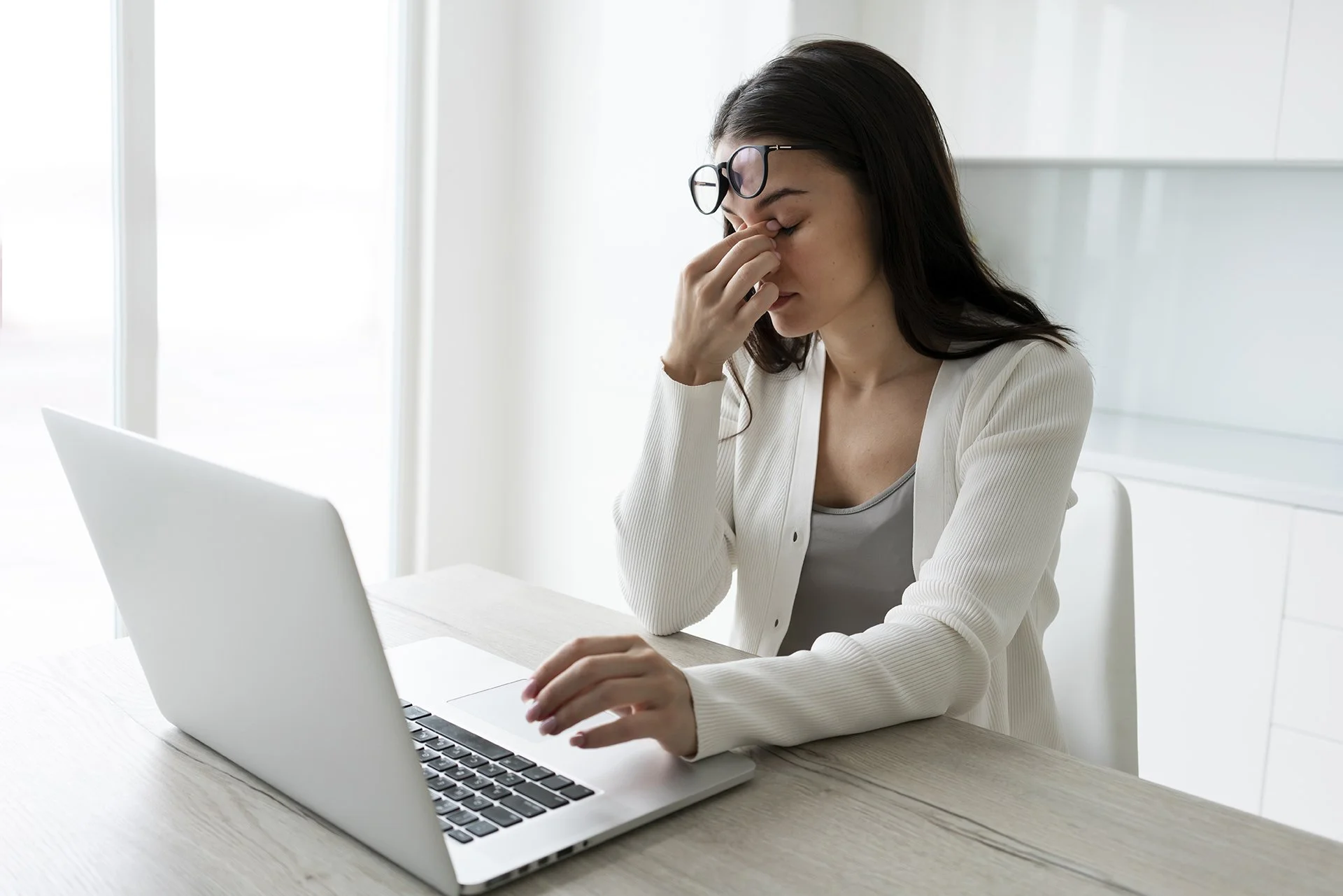